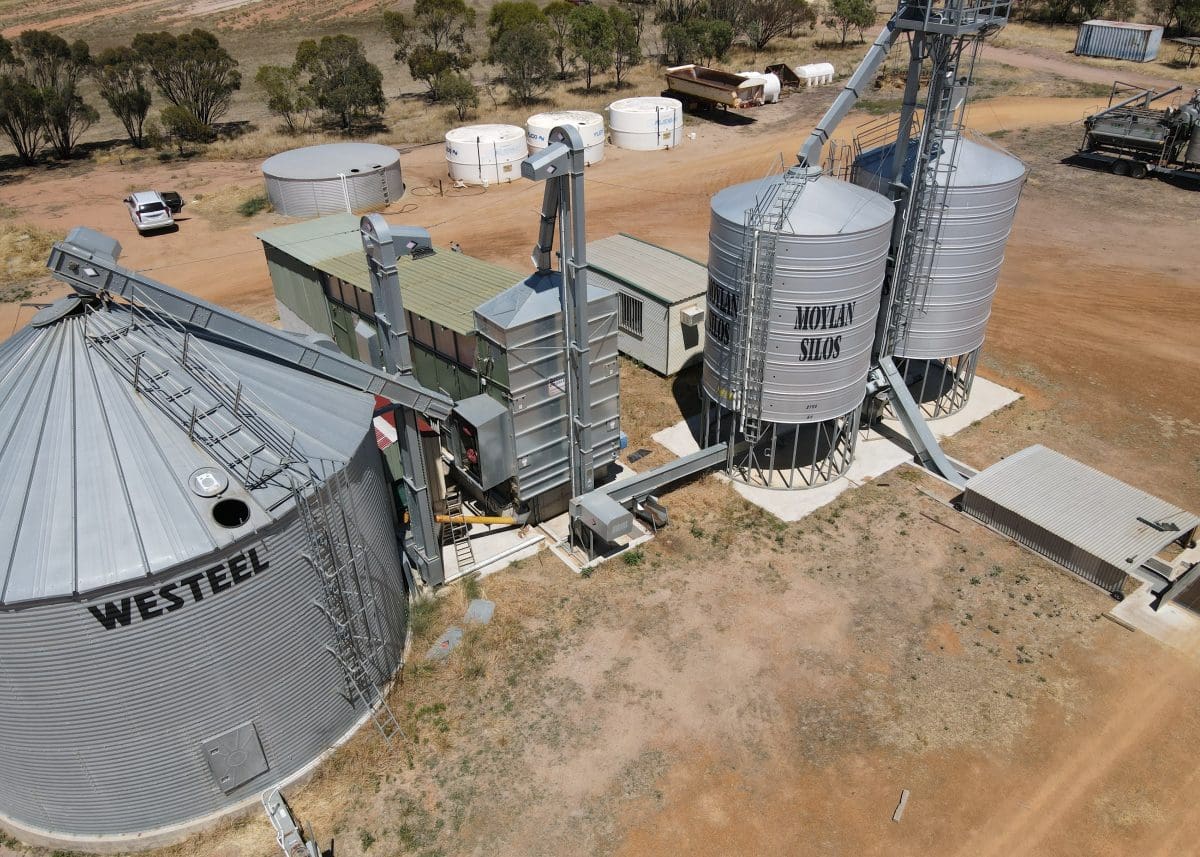
Grain dryers and associated infrastructure can cost around $500,000 but boost harvest efficiency and grain specs. Photo: Alvan Blanch
GRAIN dryers are improving efficiency for growers wanting to harvest longer and out-turn to specs faster at opposite ends of the Australian grainbelt, and at many points in between.
They are reaching into the tropics as Australia’s summer-cropping region expands, and they are helping Western Australian growers take off massive harvests including the record one just gone.
Alvan Blanch Australia and New Zealand distributor Jim Duncan said growers buying dryers do so as part of on-farm storage-and-handling systems that create flexibility needed in wet or damp harvest conditions, and to ensure quality grain can be outturned to catch the market highs.
“The investment in storage and handling is significant wherever we seem to go,” Mr Duncan said.
“We’re part of a number of discussions where people are looking to provide a bit of security around harvest.”
When used with aerated storage and enough silos to allow tonnages with different moisture levels to be blended, it means growers can deliver grain beneath maximum allowable moisture levels.
“A rain event, or a serious moisture event, does create concern, and growers now are more aware of the technologies that can help them.”
Counter for sea air
Mr Duncan said a number of Alvan Blanch (AB) dryers have been installed on farms close to WA’s south coast and used primarily for cereals and canola.
“There’s beginning to be a reasonable population of AB product in the area.”
At Jerramungup, north-east of Albany, and roughly 60 kilometres from the coast, Rex Parsons and family in 2015 installed a new AB unit to replace a smaller cascade dryer.
“That was nowhere near as flash as the one we’ve got now,” Mr Parsons said.
Following a “very wet harvest” in 2011, the family got thinking about updating and augmenting their drying capacity.
A trip to New Zealand to inspect a unit in action encouraged the family to order an AB dryer, and a consultancy working with AB conferred with the Parsons to design a set-up that fitted in with what was already on site.
That included two 75t feed silos and a 350t outloading silo.
The Parsons’ system now in use includes an underground conveyor which connects the drive-over pit as well as the grain shed with the dryer.
“We’re saying it will do about 22-26t an hour generally, and take the moisture from 14pc to as low as 11pc so we’ve got dry grain to blend.
“It gives us four to five more hours of harvesting most days, so we can start at 0730 with our two headers.
“It’s equivalent to having another header. “
The Parsons typically spend six weeks harvesting their 7000 hectares of crop, and would spend at least a week longer without the dryer.
“We’ve run it on specs to suit malting barley, and we can run it a bit hotter for feed barley.
Mr Parsons said better-quality wheat takes longer to dry, but the investment in time and operating is seen as worthwhile if it can get grain into higher grades.
The Parsons’ dryer also handles canola, and Mr Duncan said a number of AB clients in southern WA were prioritising the high-value oilseed for harvest and out-turn.
“Guys in WA were drying canola at 30-35t/hr, and taking out 2-3pc of moisture,” Mr Duncan said.
Mr Parsons said their strategy was to have some grain dried to well below maximum receival standards to blend with grain of higher moisture.
He said they were yet to utilise “the full extreme” of the dryer’s capacity, and were now working on fine-tuning the use of internal moisture sensors to regulate speed and temperature.
North-south demand
Mr Duncan said the AB units have been attracting “a lot of interest” across Queensland, New South Wales, Victoria and southern Western Australia.
The next delivery scheduled for Queensland is expected to be to Sundown Pastoral Company’s St Ronans at Forty Mile, north of Charters Towers, where it will be used to dry sorghum and soybeans.
AB units aren’t too hard to find in Central and southern Queensland and northern NSW, where summer-dominant rainfall can bring the sorghum crop home with a wet sail.
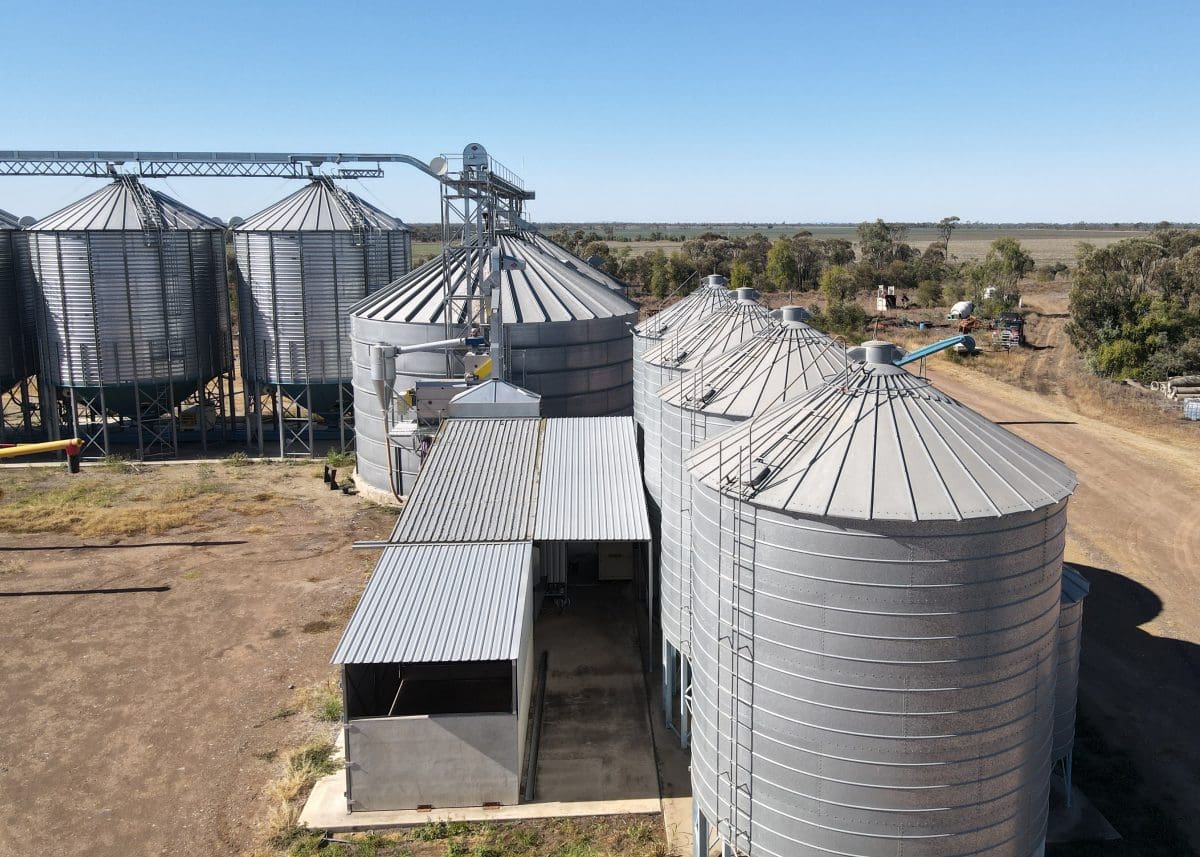
This dryer is used for sorghum in the Gregg family’s operation at Dysart in CQ. Photo: Alvan Blanch
Victorian grower Dan Coulthard bought his dryer five years ago to add value to his double-cropping system, where corn is grown over summer and cereals are grown over winter.
On the family’s farm at Peechelba East, seed crops for canola and sorghum are also grown in opposite seasons.
Mr Coulthard said he aims to put the corn into the dryer at maximum 25pc moisture, and takes it down to 15pc.
“Then it goes into aerated silos and comes down 1.5pc.”
The corn has gone to snack-food manufacturers, and the region is also a supplier of corn to the stockfeed market.
The Coulthards’ investment in a dryer came about because they switched from growing corn for silage to growing it for grain, and because of the tight turnaround between the winter and summer crops.
“When you’re double cropping in Vic, crops don’t dry down enough on their own.
“I’m pretty sure it’s paid for itself by now.”
Mid-year deliveries expected
Mr Duncan’s working relationship with AB dryers started roughly 10 years ago.
“They said: ‘We need someone to help us in New Zealand’, but to be honest, I didn’t think we’d sell one in Australia.”
Despite more dry years than we’d all care to remember, dryers keep selling, with broadacre farmers a major part of the customer base.
“During the drought from 2017 to 2019, we were selling into the nut industry, and we’ve been fortunate that producers in other industries have latched on.”
AB dryers are sold with Swedish-made Skandia elevators and conveyors, which are ordered to arrive in Australia at the same time the dryer arrives from the UK.
They can be powered by diesel or gas, with grain farms invariably going for the gas option.
Mr Duncan said other energy sources are possible.
“In Far North Queensland, a client is drying lemon myrtle leaf through a heat exchanger.”
Demand is certainly subject to seasons.
“When harvest was just getting started in WA in early to mid-November, there was a wet spell just as the headers were getting going, and our phones just lit up.”
“The end result of that is that we’ve received orders for delivery in June-July this year.
“Pre COVID, it was six months from order to on the farm and pressing the button, and now its eight and sometimes 10 months.”
Back to the 60s
The AB range starts with seed-based driers running at 2-3t/hr through to the largest units which can work through 60t/hr.
The units are manufactured at Chelworth, Wiltshire, and the company’s managing director Andrew Blanch is the son of Alvan Blanch, a grain farmer and self-taught engineer, who founded the business in 1952.
Continuing the family tradition, two of Andrew’s children are involved in the business, which moved into export in the mid-1960s and now has units in around 100 countries.
Mr Duncan said the oldest one he has found in Australia was purchased in 1966 and installed at Anchorfield at Brookstead on the Darling Downs.
It’s still going strong.
Brazil Farming principal Lyn Brazil said it has been used in probably every season year since he and wife Bobbie moved to Anchorfield 33 years ago.
“Some years we don’t use it much, and one year, every tonne of sorghum we harvested went through it,” Mr Brazil said.
An investment in an AB drier is a solid one, and Mr Duncan said the basic design with associated infrastructure costs around $500,000.
Projects with extensive associated engineering and infrastructure can hit the $2 million mark.
Grain Central: Get our free news straight to your inbox – Click here
HAVE YOUR SAY